The global aluminium smelting industry represents a significant contributor to industrial greenhouse gas emissions. As aluminium is an essential material in clean energy manufacturing and modern infrastructure development, the increasing demand for this metal has made emission reduction in primary aluminium production a critical factor in achieving global carbon neutrality. Nevertheless, the primary aluminium smelting process faces substantial challenges in emission reduction pathway design due to its enormous electricity requirements, complex production procedures, and significant variations in energy structures across different regions.
To address this problem, Professor Guan Dabo’s Research Team of Tsinghua DESS developed a smelter-based bottom-up global aluminium GHG emissions inventory (CEADs-AGE), which covers a wide range of technologies and configurations, providing a detailed assessment of emissions at the facility level. The relevant research findings have been published in Nature-Climate Change.
Power structure challenges despite significant technological progress
The study has shown that despite the gradual installation of more efficient and higher amperage cells in new aluminium smelters globally, the share of aluminium production powered by fossil fuel-based captive power units increased from 37% to 49% between 2012 and 2021, partially offsetting the mitigation effects resulting from technological progress. In 2021, we identified 91 GW of operational captive thermal power capacity, of which 70 GW was built after 2010, meaning that these units are still relatively young and are likely to remain operational for an extended period in the foreseeable future.

Fig. 1 Technology and emission patterns of global aluminium smelters and their fossil fuel-based captive power units in 2021.
Different mitigation pathways: balancing technological innovation with power system structural planning
The significant variations in electrolytic cell designs and energy structures across global aluminium smelters necessitate facility-specific mitigation strategies. This study integrates five socio-economic pathways with four critical technology deployment scenarios, constructing a comprehensive framework of 120 future scenarios. Through this systematic approach, the research elucidates both the potential and challenges of carbon reduction in the global electrolytic aluminium industry across different regions. It has been found that if the global aluminium industry maintains its current technology levels, without adopting additional mitigation technologies and with the regional electricity structure and production level following the SSP245 scenario, total emissions could reach 675 Mt yr−1 by 2050, with 22.4 Gt of cumulative emissions from 2020 to 2050.
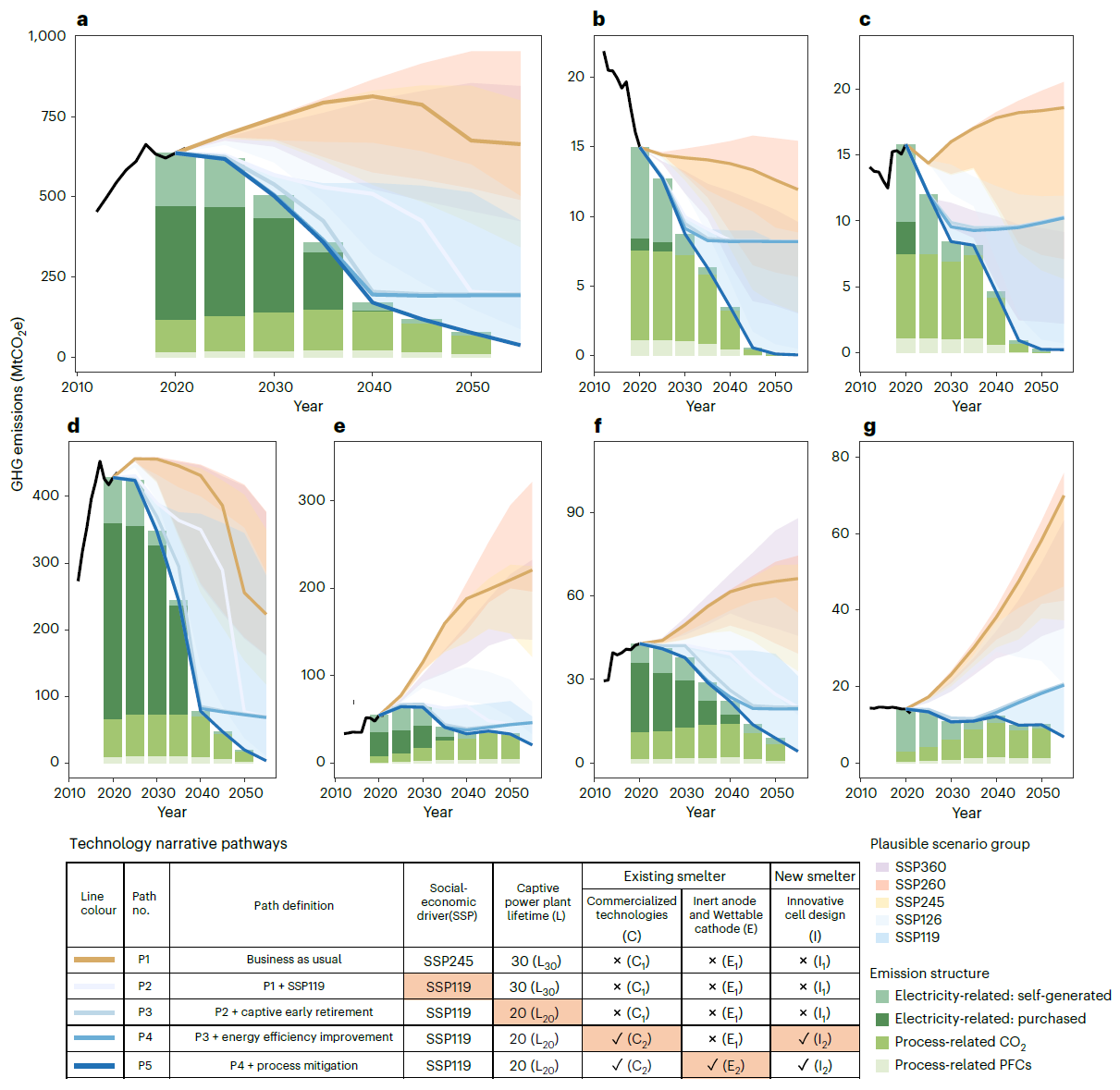
Fig. 2: GHG emissions pathways of the aluminium industry in Total GHG emissions from the primary aluminium smelting sector in global (a), Europe (b), North America (c), China (d), India (e), Middle East (f) and Africa (g).
Power decarbonization: tremendous potential yet constrained by limitations
With the gradual construction of low-carbon regional power grid, the cumulative emissions of global aluminium industry can be reduced to 15.2Gt in 2020-2050. Retiring fossil fuel-based captive power plants a decade earlier than planned (from 30 years to 20 years) could result in an additional cumulative emissions reduction of up to 3.4 Gt. Reducing the lifespan of captive power plants from 30 to 20 years would require 26% of currently operating captive power units (91 GW) to cease operations by 2030 and 53% to be shut down between 2030 and 2035.
Innovative technologies drives carbon neutralization in the industry
While power decarbonization through abated fossil fuel-based captive power plants and green grid is necessary, it is not sufficient to achieve carbon-free aluminium production. The aluminium industry is required to seek technological innovations. Implementing inert anode and wettable cathode technologies is especially crucial to reducing process-related emissions. The retrofitting of smelters with inert anode technology could reduce emissions intensity by 1.3–1.8 tCO2e t−1 Al in a current primary aluminium smelter. In different production scenarios, these new technologies could reduce emissions intensity by 5.0–10.5 tCO2e per tonne of aluminium for dependent smelters. At least 18% of smelting capacity by 2040 and 67% by 2050 must be retrofitted with inert anode technology to achieve net-zero targets.
The research puts forward combinations of facility-scale different emission reduction technologies in the global electrolytic aluminium industry, providing a scientific basis for carbon neutral pathways in different industries and regions. At the same time, the research advocates that future mitigation efforts should encompass the entire supply chain to ensure a systematic approach to decarbonization, laying an important foundation for the 1.5°C target and the sustainable development of the global aluminium industry.
Tan Chang, a Class 2021 Ph.D. student of Tsinghua DESS, is the first author of the paper. This research is funded by International Joint Mission on Climate Change and Carbon Neutrality, the National Key R&D Program of China, and the National Natural Science Foundation of China.
Full-text link: https://www.nature.com/articles/s41558-024-02193-x
Written by Tan Chang
Edited by Wang Jiayin
Reviewed by Zhang Qiang